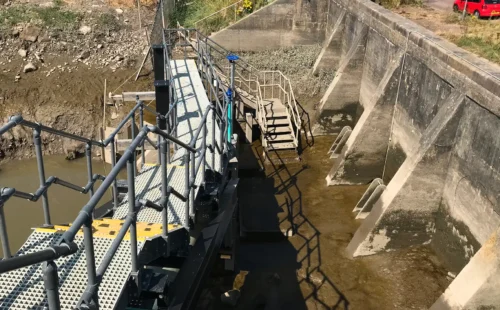
What are the best corrosion-resistant materials for infrastructure in the water industry?
From stainless steel to GRP, we take a look at which corrosion-resistant materials are best…
General Sales | +44 (0) 1255 446838
Sales Support | +44 (0) 1255 423601 (Option 5)
Transport | +44 (0) 1255 462567
Rail | +44 (0) 1255 440291
Industral & Commercial | +44 (0) 1255 440290
High-Rise | +44 (0) 1255 446830
Decking & Cladding | +44 (0) 1255 440298
Marine | +44 (0) 1255 440297
We can help you make data-driven decisions about the right product specifications for your projects and we consider all aspects within our composite product design, including aesthetics, usability, lifecycle, cost and efficiency. We’ve invested heavily in real world testing and analysis and present a range of technical information here to help ensure you get a perfect match for your needs.
In 2017, we embarked on a major programme to develop our own in-house database of composite material properties. Known as ‘Power of Composites’, the tool is the result of years of extensive research and rigorous live and simulated testing.
With ‘Power of Composite’s users can compare products across the Dura Composites range with the click of a button, with easy to interpret graphs, collated into a single view.
Once a range of suitable products has been identified, detailed product information such as drawings, dimensions, load tables and graphs unique to these products can be accessed and downloaded for analysis and approval.
Take a look at our testing related articles to widen your knowledge on our market-leading composites.
From stainless steel to GRP, we take a look at which corrosion-resistant materials are best…
In safety-critical environments, trusting the wrong test data can be dangerous. Discover why only d²…
This article explores why traditional steel is becoming less practical for water industry infrastructure due…
FRP (Fibre Reinforced Polymer) is a broad category of composites reinforced with fibres like glass,…
Test Reports
Dura Composites have undergone an artificial weathering testing regime on a number of components to…
DownloadCertificates
This is an Environmental Product Declaration in accordance with EN 15804+A2 & ISO 14025/ISO 21930…
DownloadCertificates
This Eco Report gives insights into the environmental impact of 1 Dura Composites Pultrusion Product…
DownloadCertificates
This Eco Report gives insights into the environmental impact of 1 Dura Composites Moulded Product…
DownloadOur in-house Design and Engineering capabilities help you adapt to specific challenges in complex projects, using the most sustainable composite solutions available. Meet some of our experts below.